
The Combus surface finishing plant - part of the Testi Group - uses machinery from Breton S.p.A. for resin treatment as well as polishing of marble slabs.
The quality of a natural stone's final surface polish is dependent on many factors, including the equipment being used, the products employed during the process and the skill of the processor. And in order to maintain an optimum level of quality, Testi Group has dedicated its “Combus†division to work solely on finishing the surface of marble slabs.

Prior to being treated with the resin, slabs are placed in an oven that is heated to 50 to 62 degrees C to remove all humidity from the material. This allows for maximum efficiency of the resin, and each oven can hold 42 slabs.

Resin products from Tenax S.p.A. are critical to the process. Generally, Combus uses Tenax's Protex sealer, which is formulated to reinforce porous stones and also offers oil protection.
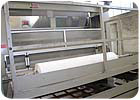
In addition to resin reinforcement, fiberglass netting is applied to the slabs as needed.

On average, Combus processes one slab every two minutes.

After the resin cures, the slabs receive their final polish on a 14-head Levibreton polisher from Breton S.p.A.