
After decades in the countertop business, Innovative
Surfaces of Hastings, MN, expanded into stone fabrication, and it invested in
the latest stoneworking technology.
For Bruce Akins, owner of Innovative Surfaces of Hastings, MN, the transition from laminate countertops to stone fabrication was nearly 30 years in the making. And when the company decided to make the expansion into natural stone and quartz surfacing, it did so with the latest generation of stoneworking technology.
“I personally started in the countertop business in 1974 working for a laminate fabricator,” Akins explained. “In 1988, I started my own business and went from laminate fabrication to solid surface fabrication. In the late 1990s, we began installing quartz products, but outsourced the fabrication. We started fabricating our own natural stone and quartz products in 2003.”

>Innovative Surfaces’ stone fabrication shop is
equipped with a range of equipment from Park Industries of St. Cloud, MN.
As the company’s business grew, it added a second Destiny CNC stoneworking center as well as a Park Industries Titan CNC stoneworking center and a Park Industries Fastback edging machine. Innovative Surfaces also invested in some of the newest technology from Park Industries, including the Fusion 6000 combination bridge saw/waterjet and the Pathfinder laser layout-projection workstation. Akins said that these latest investments have added a new level of efficiency to the operation. “The Fusion has been great. We’ve had a lot better material utilization and it has relieved some time on our CNCs,” he said. “We have more machining time available on our CNCs. We bought the Pathfinder at the same time, so all slabs are photographed and laid out prior to being cut.”

The company operates two Destiny CNC stoneworking
centers as well as a Titan CNC stoneworking center.
“Our business is wholesale, so clients of our customers come to us after we’ve taken photos of the slabs, and view the photos and slabs for layout approval,” Akins explained. “It’s nice to be able to view and manipulate the pieces prior to cutting.”

More recent investments include a Fusion 6000
combination bridge saw/waterjet from Park Industries.
Water used during the fabrication process is treated using an EnviroSystem from Water Treatment Technologies of Hampton, NH. “We started in 2003 with Water Treatment Technologies, and we upgraded the system a couple of years ago,” Akins said. “When we started in 2003, we were maybe doing three kitchens per day, and we peaked at 10 to 12 kitchens per day.”

“The Fusion has been great,” said Bruce Akins of
Innovative Surfaces. “We’ve had a lot better material utilization and it has
relieved some time on our CNCs.”
When bringing in new employees, Innovative Surfaces generally educates workers from the ground up. “We do our own training, and we typically don’t bring in machine operators,” Akins said. “We want people to understand hand finishing and our expectations of the finished product first before they become a machine operator. In our area, there aren’t a lot of people who run equipment looking for work.”
The client base at Innovative Surfaces is primarily comprised of retailers, kitchen and bath dealers, remodelers, contractors and commercial millwork shops. Akins described the current business climate as “soft” in terms of sales. “It hasn’t gone away, but it is challenging,” he said. “There is some work out there. Our quoting activity has picked up, but it hasn’t related to sales yet. That’s just part of the current economy. People are getting ready to do projects, but they’re not quite ready to pull the trigger yet. We’re hoping it’s a sign of what’s coming down the road.”

The company has a total of 65 employees, including 30
workers in the stoneworking operation.
As testament to the company’s dedication to quality, it is among the first group of fabricators in the nation to receive accreditation from the Marble Institute of America (MIA). This distinction is reserved for residential-oriented companies that have been in business a minimum of three years, have successfully completed 200 projects in those three years, have 2,000 square feet of dedicated fabrication space and have passed a voluntary or mandatory OSHA facility inspection in the previous year, among a host of other standards.
Sidebar: Innovative Surfaces
Hastings, MNType of work:residential kitchens (65%) and commercial work (35%) in natural stone, quartz surfacing and other materials
Machinery:Wizard radial arm polisher, Pro-Edge automated edging machine, two Destiny CNC stoneworking centers, Yukon bridge saw, Titan CNC stoneworking center, Fastback edging machine and Pathfinder laser layout-projection workstation, all from Park Industries of St. Cloud, MN; EnviroSystem from Water Treatment Technologies of Hampton, NH
Number of Employees: 65, including 30 employees dedicated to stone and quartz surfacing
Production Capacity:10 to 12 kitchens per day, in addition to commercial work

Sidebar: The Artisan Group
Innovative Surfaces is part of the Artisan Group, a national organization of 36 independent granite fabricators that have joined together to offer the Artisan Stone Collection, the first and only brand of granite wholly owned by Artisan Group, which has a comprehensive lifetime warranty. The group also offers Heritage Wood countertops and Kohler sinks and faucets.Group members average more than 20 years of fabrication experience in the countertop industry. Moreover, all Artisan Group members have achieved - or have begun the process to achieve - full accreditation with the Marble Institute of America. The group is among the first granite fabricators in the world to be working towards this distinction. Collectively, they surpassed $250 million in sales in 2008.
Artisan Group also provides a complete line of granite care products including: Firstline Sealer, Firstline Clean & Restore and Firstline Shine.
“When we started buying stone, we got involved with AG&M Granite of Austin, TX, and became involved in the Artisan Group,” explained Bruce Akins of Innovative Surfaces. “It’s nice brand recognition. We think it’s elevated the brand awareness of granite to the point where it isn’t so generic. It has taken away some of the commodity image, and we hope people look at it differently.”
Additionally, Akins said he is able to rely on the collective experience of the group’s members from a practical perspective. “It’s a great group of people to speak with and share information,” he said. “There’s really a wealth of knowledge there.”
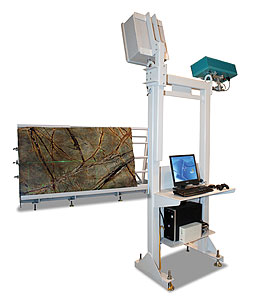
When the company added the Fusion 6000, it also
invested in a Pathfinder laser layout-projection workstation (an example of
which is pictured). Using a DXF file, the Pathfinder projects a laser on the
slab, and the projected image can be moved over the portion of the stone to be
used and adjusted to achieve optimal production.
Additional Photos

Innovative Surfaces has a full-scale showroom to host
clients in the greater Twin Cities region of Minnesota.

Innovative Surfaces processes an average of 10 to 12
kitchens per day, in addition to commercial work
