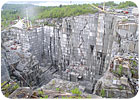
Rock of Ages Corp. acquired the E.L. Smith Quarry in Barre, VT, in 1947. Emery L. Smith -- a native of Northfield, VT -- originally opened the quarry around 1880.
Barre, VT, has long been known for its fruitful supply of Barre granite. The industry particularly witnessed explosive growth when the first railroad -- known as the “Sky Route” -- was built in town in 1888. And leading the charge among local granite producers was Boutwell, Milne & Varnum Co., which eventually evolved into what today is called Rock of Ages. Presently, the company owns 10 quarries throughout the U.S., Canada and Ukraine, including the E.L. Smith Quarry in Barre, VT.
In 1930, Rock of Ages Corp., which was founded by James M. Boutwell, George B. Milne and Harvey W. Varnum, purchased 10 of the largest and oldest granite manufacturing companies in Barre -- establishing itself as the largest quarrier and manufacturer in the region by bringing more than one-third of all of Barre’s production under one roof. The company then further expanded its quarrying capacity in 1947 when it acquired the E.L. Smith Quarry and the Wetmore Morse Co.
Emery L. Smith -- a native of Northfield, VT -- opened the E.L. Smith Quarry around 1880. A number of quarrying innovations can be credited to Smith, including the first person in Barre to use a fixed derrick for lifting blocks; the first to use electric batteries to detonate explosives; and the first to use compressed air for drilling.
Today, the site covers a surface area of 50 acres and is about 600 feet in depth. It is believed to be the world’s largest dimension “deep-hole” granite quarry, according to Rock of Ages. Additionally, it accounts for approximately 75% of the total production of Barre granite quarried each year.
The majority of blocks pulled from the E.L. Smith Quarry range from light to medium shades of Barre Gray. While some of the granite quarried is not suitable for use as a finished product due to cracks, spots and other natural imperfections, the recovery rate at the E.L. Smith Quarry is quite high at 75%.
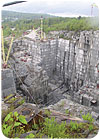
Today, the site covers a surface area of 50 acres and is about 600 feet in depth. It is believed to be the world’s largest dimension “deep-hole” granite quarry, according to Rock of Ages.
Quarrying equipment
Large derricks -- ranging from 110 to 160 feet tall and capable of lifting 250 tons each -- are used to lift granite blocks and transport workers around the site. The derricks are driven by electrically powered hoists, which are located in small buildings called “hoist houses.” These houses are placed at various distances from the base of each derrick and are operated by skilled workers known as “hoist engineers.” There are also “derrickmen” who stand at the railed areas near the edge of the quarry, and use an intricate set of hand signals to relay information from the workers at the bottom of the quarry to the engineer in the hoist house.Additional equipment at the E.L. Smith Quarry includes Tamrock Slot Liners with #600 hammers for channeling and #550 hammers for drilling deep holes and Tamrock Zoomrails for block trimming. Also, Pellegrini wire saws -- both diesel and electric -- are used in the quarrying process.
To free a large granite mass vertically from the quarry, a channel is cut. The average-sized piece channeled from the wall is about 40 x 30 x 17 feet. Pneumatic equipment is then used to drill holes horizontally at the base of the mass -- approximately 6 inches on center. Explosives are then placed in these holes, which are called “lift holes,” and detonated to free the channeled mass.
The next step is to drill deep along the “hardway” to break up the large, channeled mass into smaller “line” granite from which standard-sized saw blocks can be cut. Once the “hardway” line is broken free, the resulting pieces are ready to be cut into standard-sized blocks. This procedure is accomplished by drilling a series of holes of 3/4-inch diameter about 3 inches apart. Plug wedges and shims are then inserted and driven in with an 8-pound sledgehammer to split the block free.
In total, Rock of Ages employs 750 employees, of which 150 are in its quarry division. There are about 40 workers at the E.L. Smith Quarry, which produces approximately 1,200 cubic meters of Barre Gray per month. According to the company, it can increase its production capacity upon demand.
Primarily, Barre granite is used for monuments and memorials. At the time of Stone World’s visit to Rock of Ages’ processing plant, workers were making a monument for a park that sits below the “Old Man in the Mountain” in New Hampshire. Being one solid block that weighs 180 tons, this will be the largest block of granite used in a monument, according to the company. Most of the waste material left from the quarrying process is crushed and used for roadwork.