
Visitors approaching Yale University's Peabody Museum of Natural History in New Haven, CT, are greeted by a life-sized bronze Torosaurus statue, created by Peabody Museum Preparator Michael Anderson and a team of paleontologists, zoologists, artists and volunteers. The 21-foot statue sits atop a 95-ton base of Stony Creek granite, which was designed by sculptor Darrell Petit.
Visitors approaching Yale University's Peabody Museum of Natural History in New Haven, CT, are now greeted by a striking figure on the building's east side - a life-sized bronze Torosaurus statue, created by Peabody Museum Preparator Michael Anderson and a team of paleontologists, zoologists, artists and volunteers. The 21-foot statue sits atop a 95-ton base of Stony Creek granite, and the stone's raw and distinguished form was sculpted through a combination of natural geology and the resourcefulness of sculptor Darrell Petit.
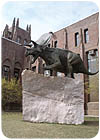
The granite base is comprised of three separate elements that come together to form the whole, and the stone's raw form reflects the natural processes that created it millions of years ago.
“[The Peabody Museum staff] approached me with a 12-inch-high Styrofoam model of what they wanted for the base element and asked if it would be possible. They were looking for a large triangular shape that protruded out dramatically like a ship's prow,†Petit explained. “I wanted to first see if the form existed within the quarry formation and if we could attain it by quarrying around it. It took one year to find the spot in the Level 7 sector of the quarry that would yield the right shape. The original model was more of a simple geometric wedge. We quickly educated Michael Anderson in the creative possibilities within the quarry process itself, and then we proceeded to go for it.â€
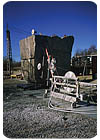
One of the goals for the project was to retain the natural feel of the base, and to make sure it would not appear as a manufactured, processed pedestal. The only element of the base that reveals human intervention is the back. “We knew that it would accommodate a plaque, so we used a wire saw and then had it sandblasted,†Petit said.
Extracting the stone
From the beginning, one of the goals for the project was to retain the raw natural beauty of freshly excavated granite of the base, and to make sure it would not appear as a manufactured, processed pedestal. “It is a sculpture composed of two elements - the dinosaur and the sublime force of nature,†Petit said. “We didn't want to tame one to be subservient to the other.â€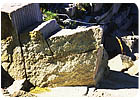
“I wanted to first see if the form existed within the quarry formation and if we could attain it by quarrying around it,†explained Petit. “It took one year to find the spot in the Level 7 sector of the quarry that would yield the right shape.â€
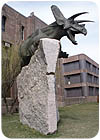
The front of the base resembles a ship's prow, and the shape of the top granite piece complements the shape of the Torosaurus' head.
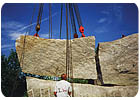
The three pieces of the base were fitted with 4-inch-thick steel lugs, and they were lifted using a 250-ton crane. Each piece was lifted on three points, and each of the points could be moved independently --- similar to the way a “Sicilian string puppet†is maneuvered from above, Petit explained.
The only element of the base that reveals human intervention is the back, which faces the small strip of land between the statue and the museum itself. “We knew that it would accommodate a plaque, so we used a wire saw and then had it sandblasted,†he said.

Photos copyright Anita Soos. Throughout the project, Marino Crane was responsible for the engineering, rigging, logistics and transportation.
Transport and assembly
The three pieces of the base were fitted with 4-inch-thick steel lifting lugs, and they were lifted using a 250-ton crane. Each piece was lifted on three points, and each of the points could be moved independently - similar to the way a “Sicilian string puppet†is maneuvered from above, Petit explained. “We needed to be able to maneuver this way because each piece had to fit perfectly; every convex or concave angle of each piece needed to fit with the angle on the connecting piece. Marino Crane was instrumental in rigging and moving the three elements, and they also got involved in the engineering. We really wanted to save the natural form of the stone, and we didn't want the edges damaged. Marino Crane utilized a three-dimensional modeling program to ascertain the center of gravity of each element and to determine the exact picking points so pieces could be picked.â€
Photos copyright Anita Soos. The base had to be further worked by Petit after it was delivered to the site. “For me, it was a precedent project that I wanted to be involved with,†Petit said of his work on the venture.
Once at the site, a major concern was spreading the load properly, and the site had to be prepared to accommodate the weight of the statue and base, since there was infrastructure underneath.
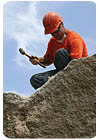
Photos copyright Anita Soos.