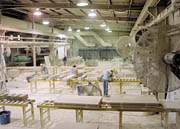
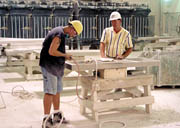
"We wanted to solve these problems and create a more comfortable and pleasant environment for the 17 to 25 employees who typically work in this area," said ILCI General Manager George James. "These artisans are carrying on a tradition of hand craftsmanship that has placed the company in the forefront of dimensional stone fabrication for more than 66 years." The company has handled some of the most prestigious construction projects in the country, including the Empire State Building, the National Archives Building and the Willard Hotel, among others.
James explained that ILCI, which produces approximately 1 million cubic feet of merchantable quarry volume annually, had tried other methods in the past to rid the factory of dust, but they were unsuccessful. "After buying and using dust collectors that failed to clear the air, and carefully researching other options, we found a solution using a high-efficiency cartridge collection system designed by Air/Pro Inc. and manufactured by Farr Air Pollution Control (APC)," he said.
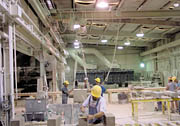
Searching for the solution
Several years ago, ILCI invested in a network of dust collectors that were connected to movable source-capture hoods placed in areas of high dust generation. ut given the heavy concentrations of dust in the large cutter bay, which measures 140 feet long x 68 feet wide x 20 feet high, source capture was not effective, and the system was eventually shut down.ILCI management wanted to stay on top of increasingly stringent OSHA regulations, which limit the allowable level of nuisance dust to 5 mg. per cubic meter of air. We use wet collection to handle dust in other areas, so we investigated the possibility of knocking down the dust with water and channeling it into our existing water cleaning system," said James. "But when we did the math, we found that the horsepower required to accomplish this would have been off the charts."
In seeking a more practical solution, ILCI contacted Air/Pro Inc., a Cincinnati-based firm that specializes in problem solving for industrial air moving, air cleaning and pollution control applications. "Looking at the room dimensions, we thought in terms of treating the space as a tunnel - placing the collectors at one end and sweeping the air up above workers' heads, across the length of the room, and into the dust collectors," explained Tom Woods, a sales engineer with Air/Pro. "In addition, the customer wanted to re-circulate the cleaned air back through the work bay to prevent energy loss during the winter months, when the room is heated to a constant temperature for worker comfort. So we designed a system of ductwork to return the air to the other end of the room in a circular pattern."
According to Woods, the concept is based on modular booth-type collection systems that are popular for self-contained areas where source capture is not practical, and hoods could interfere with worker productivity. "This area was too large for standard air quality booths, so in effect we custom designed our own version," said Woods. To filter out the dust, Air/Pro selected the Farr "Gold SeriesR" collector, a cartridge collection system with a modular configuration that lent itself well to the design.
The system utilizes four identical collectors with 16 cartridges each, in a shallow configuration of two cartridges deep by eight cartridges wide. This arrangement takes up most of the 68-foot south wall, while occupying minimum floor space. The filters have a patented design that provides 425 square feet of media in each cartridge, meeting the total 67,200 cfm airflow requirement with a much smaller housing than conventional cartridge collectors, while also delivering high-filtration efficiency, excellent energy performance, and long element life. "We liked all these features, as well as the rugged construction of the collectors," said Woods.
Farr APC worked closely with Air/Pro to customize the collectors as needed to fit ILCI's unique requirements. The manufacturer built baffles into the heavy-duty 10-GA access doors to allow dusty air to enter the cartridge area of the collectors directly through the doors. They also designed special dust pans to fit into the bottom of each module for easy removal of the captured dust.
To ensure adequate airflow through the room, Air/Pro used customized direct drive fans on the units, sized for the collectors and for system static pressure requirements. They also advised ILCI on the need to place auxiliary fans strategically through the room to accelerate the air and help direct it toward the collectors. ILCI closed the outside truck doors and added curtains and flaps to seal off other internal openings to isolate the area being treated, again ensuring that the desired air circulation within the space would not be compromised.
Air/Pro handled the design, engineering and installation of the dust collection system on a turnkey basis for ILCI - including the collectors, custom fans, special control packages, ductwork and other components. They performed the majority of the installation during a scheduled plant shutdown to avoid disruption of cutting operations.
The result
The resulting system exchanges the air about 20 times an hour, constantly cleaning the air and making sure dust never lingers for long in the nearly 200,000-cubic-foot space. "It's quite obvious that everyone has seen a big improvement since we installed the dust collection system," said James. "The air is significantly less dusty, and visibility in the room is much improved. It's a much better working environment, and it keeps us well within OSHA limits for nuisance dust."Moreover, James reports that the dust collection system has delivered additional advantages - some of them unanticipated:
Energy efficiency: Despite the rapid air movement and the new equipment required to move and clean that air, James describes the effect on ILCI's energy bill as "negligible." "The equipment is very energy efficient, and we only operate it during one shift," he said. "Also, by re-circulating the air, we conserve energy throughout the heating season."
Reduced equipment maintenance and downtime: The improved cleanliness of the ambient air has been beneficial to other equipment in the work area. The one million BTU heaters used in the room formerly needed maintenance and cleaning every two weeks, including frequent replacement of electronic components. The dust collection system has eliminated that problem, and has also lessened maintenance requirements for the large cranes used to move stone within the room.
Longer tool life: "In order to provide the clean, dry air needed to pulse dust off the filters, we had to clean up and rebuild our existing compressed air system," said James. "Now that the system is delivering cleaner, oil-free air, pneumatic tools and components are lasting four to five times longer. We quickly saved about $5,000 in drill replacement costs, and even more for costly air saws."
Low collector maintenance, long cartridge life: The collectors require little or no maintenance, except for emptying the dust bins when they become full. After a full year's operation, the pressure drop in the system is still well within specifications. ILCI anticipates that they will only need to change the filter cartridges every two years. When filter replacement is needed, the collectors have a patented cambar system that will allow fast cartridge changeout with no tools required.
Currently, the captured dust is disposed of together with other stone waste, but ILCI is having the dust analyzed to see if it meets pharmaceutical-grade specifications. If it does, they will be able to sell the reclaimed limestone dust and receive even faster pay-back from their dust collection investment.