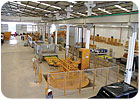
Earlier this year, Antolini Luigi & C. opened the doors to Antolini do Brasil, a state-of-the-art stoneworking facility located outside of Vitória, Brazil.
When mentioning the top stone-producing firms in the world, the name Antolini Luigi & C. is virtually always part of the discussion. Recently, the company has added a new component to its empire with the completion of its state-of-the-art slab-processing plant near Vitória, Brazil.
The new plant, which is named Antolini do Brasil, spans across 100,000 square meters (nearly 1.08 million square feet) of space, and there is room for expansion of another 200,000 square meters (nearly 2.16 million square feet) in the future. The facilities include seven buildings, three for stocking materials and four that house the stoneworking facilities.
Blocks are processed on six gangsaws from Gaspari Menotti of Italy. Four of the gangsaws have a working width of 5 meters, while the remaining two have a larger width of 6 meters. The gangsaw building also has space to add five more units in the future, as demand dictates.
The factory for slab production is equipped with automated, state-of-the-art machinery from Breton S.p.A. of Italy. When raw slabs are delivered from the gangsaws, they are first processed on a Levibreton calibrating machine, which has 13 working heads. From there, the under-vacuum resin-treating process begins. Slabs are automatically delivered to a large drier (oven), which can hold 40 slabs at one time. These driers create an environment where the surrounding air is actually drier than the ambient air humidity, which allows for maximum efficiency in applying the resin to the slabs. After the slabs leave the oven, the resin product is automatically applied to the material. The slab then enters the under-vacuum process before entering a second drier, which speeds the curing process of the resin.
After the resin-treated slabs have cured, they are automatically transported to the polishing line, where materials receive their final surface polish. The centerpiece of this line is a Levibreton KG 3000 Ultrix polishing unit, which features 22 polishing heads. The KG 3000 Ultrix is considered to be the latest generation of slab-processing technology, and it was designed to work with optimal speed and quality. In terms of speed, for example, the bridge moves at a rate of 60 meters per minute, and the working heads are lifted and lowered from the slab in less than a second. Meanwhile, the patented polishing heads have been engineered to result in a high-quality and uniform polish. The working pressure of each individual head is electronically controlled by PC and displayed on the color touch-screen control panel. This control panel also displays the speed of the machine, the bridge movement and other important data.
In terms of the site of the stoneworking plant, Antolini has taken major steps to eliminate environmental impact. In just one example of this, water is treated using a large-scale system from Fraccaroli & Balzan of Italy.
Antolini do Brasil opened its facility with a total of 50 workers, but it will ultimately employ up to 100 once it is in full production. Amenities such as an employee kitchen, dining area and comfort station with showers serve to benefit the workers. There is also an entire structure dedicated solely to machine maintenance and spare parts.
Currently, the factory is exporting 80 containers of stone per month, with North America as the primary export target. When the factory reaches full production, it will be exporting about 200 containers per month. The slab warehouse is roomy and well lit, allowing for efficient selection of slabs, and a broad variety of materials are on display. Before being shipped, material is inspected to ensure that it meets the company’s strict quality-control standards. “Marketing is important, but we make sure we start with good stone, and then follow that with good manufacturing,” explained Francesco Antolini.