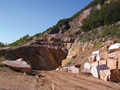
Essegri Marmi is a producer of Breccia Pernice, which
is quarried in the Volargne stoneworking region of Northern Italy.
While the beginning of Essegi Marmi dates back to 1963, the ownership’s family history in the stone industry can be traced to the 1600s. Specializing in the quarrying and production of Breccia Pernice, Essegi Marmi is located in the Volargne stoneworking region of Northern Italy. The company has supplied its unique material to high-profile projects around the world such as Trump Tower in New York City.
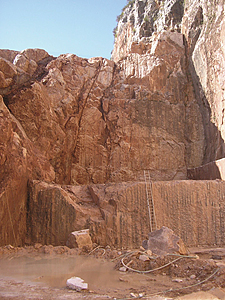
The Breccia Pernice quarries developed along a large
fault in the mountain known as the “tectonic zone.” The fragmented material is
offered in three variations, which include Chiara (clear), Medio (pink) and
Classico (red).
Savoia went on to explain that the translation for the Italian word Breccia is “fragmented rock.” Breccia Pernice is composed of fragments of red, pink and white limestone, and it is alternately referred to as a marble or a limestone. “In a sense, it is a new material because it was discovered in the early 19th century,” he said. “It is new compared to Rosso Verona. “It’s similar to the red French limestone that was used a lot for churches at the time. It competed with that.”

At the time of Stone World’s visit, Essegri Marmi was
quarrying its Medio and Classico varieties.
The material consists of different-sized fragments - both small and large. “They are not round,” said Savoia. “They are irregular - usually angular.” And due to Breccia Pernice’s low resistance to the freeze/thaw cycle, it is better suited for interior applications, according to Savoia.

Blocks are cut with a diamond wire saw in
approximately one hour.
The Breccia Pernice quarries developed along a large fault in the mountain known as the “tectonic zone,” according to Dott. Geol. Annapaola Gradizzi, an Italian geologist. “When you move from the fault, which is the heart of the quarry, the material gets lighter in color,” she said.
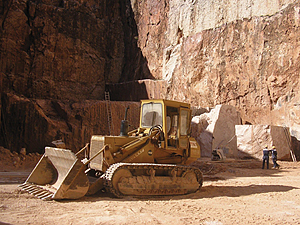
The Breccia Pernice quarries operate year round, with
between four to five workers on site.
During Stone World’s trip to Essegi Marmi’s Breccia Pernice quarries, the company was not producing the light-colored variety of the stone because it was deep inside the mountain. On average, a typical quarry face consists of 20 meters of Classico, 50 meters of Medio and 20 meters of Chiaro.

While initially large blocks are extracted from the
quarry, they are then cut into smaller blocks that are transported to the
production facility. On average, the blocks measure between 2 and 2 ½ meters.
To extract the Breccia Pernice from the quarry, the company uses a “soft blast” technique. A hole is first made with a drilling rig and then a soft blast is put inside the hole. The rest of the cuts are made with a diamond wire saw.
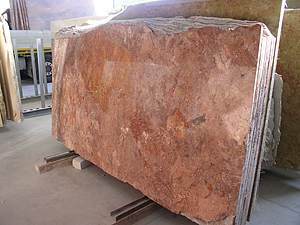
Breccia Classico is deep red in color, and it is
located in the heart of the quarry - closest to the fault.
In total, a diamond wire saw can cut a block in about one hour. The large blocks are then cut into smaller blocks that are transported to the production facility. On average, the blocks measure between 2 and 2 ½ meters.
Essegi Marmi operates its quarries year round. Typically, there are four to five workers on site. Once a quarry is no longer used for extraction, some are re-filled with waste and used for agriculture, including vineyards.
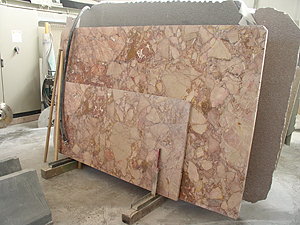
Chiara, which means “clear” in Italian, is light in
color.