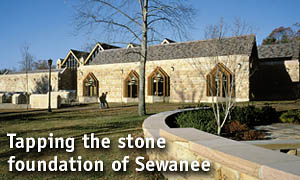
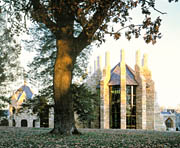
The process for creating a new building began several years ago, when the university's administration decided to unify its dining halls into one large facility. "The University had a number of places where they provided food service," explained HHPA Founding Partner Malcolm Holzman, FAIA. "They wanted to bring the dining together in one location, because they thought it would have a positive effect on the campus community. Since the University is in a remote place, everyone could eat together, and they also could get the faculty involved."
The new facility, which is 43,000 square feet in size, includes two major dining areas as well as a series of secondary spaces, including a formal 450-seat dining room, a 250-seat informal dining area, a servery, a state-of-the-art kitchen, meeting rooms, and support and administrative spaces. The building is situated at the heart of the inner campus, where the university's historic All Saints' Chapel and other significant structures are located.
Given the rich history of the campus, the design of the building was the subject of discussion and debate among the university community, including the faculty and administration as well as the students. "Everyone on campus had something in mind," Holzman said. "When I was selected to design McClurg Hall, there was the question of, 'Could this be a Gothic building?' We had a very interesting series of conversations about Gothic architecture. I didn't really think that they wanted a centuries-old Gothic building. I also didn't think they wanted the 1920s version of Collegiate Gothic, which had become a favorite stripped-down style of the 1980s and '90s. The campus and buildings had been inspired to a certain extent by English universities like Oxford and Cambridge. They aspired to that academic tradition, so the notion that they could aspire to the Gothic was what I suggested they could do."
According to Holzman, carrying out this design goal meant using natural stone. "The most glorious Gothic buildings that I know are stone," he said. "And, in fact, the majority of the buildings on this campus are stone. Certainly, the ones that are revered the most. I went to the interview with a block of stone because I had been to the campus before, and this material was in my vision for the new project."
The stone that composes much of the campus building - referred to as Sewanee stone - was actually quarried right on the Cumberland Plateau. "The stone had been quarried on the Domain, which is what they call the campus, in a serious way until 50 years ago, and to a lesser extent up to 20 years ago," Holzman said. "The only stone that they were quarrying from the Domain at the time of our design was to patch and repair buildings. They were buying sandstone from other suppliers in Tennessee. In fact, the block I brought to the interview came from one of those suppliers."
The decision to use the local stone came fairly early in the process. "We had a lengthy time period to define the program and what the students would like to have in this new dining facility, because it is only once every 25 or 50 years that an institution gets to make a building like this. One important directive that came from the students and building committee was their desire to have a refectory, a formal dining area based on an English tradition," Holzman said. "During those sessions, we started to discuss stone. Since it was next to All Saints' Chapel, the most significant structure on campus, they wanted to be sure that a new building wouldn't overshadow the chapel. But they also wanted a building that would be worthy of some attention in its own right."
During one of these meetings, stonemason Houston King, who first began working on the campus in the early 1970s, approached Holzman with the idea of using local stone for McClurg Hall. "That started the process," Holzman said. "It is slightly different than stone that comes from other parts of the state. The color is different, and the veining is quite spectacular. It is out of the ordinary."
The stone from the campus does not come from a single quarry pit, like traditional sites for granite or marble. "It actually comes from a series of ledges. Gaining access to those ledges, where the material can be extracted, is the problem," Holzman said. "Material actually came from a number of different locations on campus. I remember the first piece of stone that Houston took out. He hooked a big saw up to the axle on his truck, and used the engine to run the saw. This is not how the material was finally extracted. It can be a rather rudimentary operation to get the blocks out, to cut and split them."
According to King, ledges of useable stone are scattered throughout the 10,000-acre Domain. "We actually had three quarry sites where we pulled the stone for McClurg Hall, but there are hundreds around," he said. The stone was extracted from the ledges using air drills, followed by the traditional feather-and-wedge method of quarrying.
Once the blocks were pulled, they were processed on a wire saw that had been sitting on the campus for decades. "The old wire saw fired right back up," King said, adding that it was updated with diamond wire to improve its performance. "We also set up a saw at the quarry, where we sawed blocks. We designed that saw with old elevator rails that were taken from the library on campus."
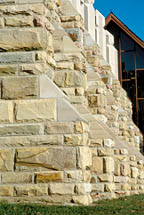
Securing the stone
According to Holzman, the design of McClurg Hall aspires to the Gothic in three basic ways: through its use of stone, its emphasis on the vertical, and by the inclusion of natural light in an unusual way. The sandstone was used to compose the majority of the building, and it was utilized in the form of rough-hewn blocks with tooled edges."The masonry was used to show off its irregularities," said Holzman. "One of the nice properties of this sandstone is that there are no pieces that are the same. You can't be embarrassed by that. You need to think that it's a virtue. The basic building units were as big as possible, while still allowing one or two masons to handle each block. There is a scale and magnitude that comes with blocks this size that provides the sense of gravity and permanence that I think you associate with stone."
The standard block was 16 inches high by a minimum of 7 inches thick, according to Robert Almodovar, AIA, HHPA Senior Associate. "The minimum bed depth was about 7 inches, but the projection was 7, 8 or 9, and in some cases, 12 inches. It was high relief," he said. "Then there were some stones that were cut into specific shapes, but the vast majority of stones - maybe 75 to 80% - were split-face, and the other 20 to 25% were cut."
In addition to serving as exterior cladding for McClurg Hall, the Tennessee sandstone was used inside of the facility. "The stone is brought into the building so that in the dining areas, individuals actually have the experience of eating next to this material," Holzman said. "It provides the sense that even when you're in the building, you understand what the building is made of. It's not like the 1920s Collegiate Gothic buildings, where the skin of the building is stone, and the inside is plaster."
While utilizing sawn stone from the campus was an attractive option, it was not a simple task. The project required a total of 2,250 tons of material, which was a daunting figure considering the small amount of University staffers on the project. "One concern everyone on campus had was whether quarrying the entire quantity of the stone from the Domain was possible," Almodovar said. "As it turned out, they worked with other quarries in Tennessee."
Approximately 40% of the stone was quarried on campus, with the remaining 60% coming from the Crossville area of Tennessee, according to King. Because of the differences between the Sewanee stone and the stone that was brought in from outside sources, the placement of finished blocks had to be carefully monitored. "In some cases, it may be more pink. In other cases, it may be more tan. In other cases, there might be greater veining through it," Almodovar said. "Because there was a range, we wanted to make sure that when the stone was installed in the building, the full range would be apparent. We didn't want to place all the brown stones in one area and all the pink stones in another area. We were very careful about the installation process when the masons began. They took care to not isolate one type of stone in one area." The material not only differs based on the quarry site, but it also ranged within a single quarry. "It varied if you went down 3 feet, or if you went down 5 feet," explained Almodovar.

Fabrication work
When it was time to fabricate the stone, the various parties involved with the project had to carefully coordinate efforts. "We had a standard shop drawing process, except the University had to hire outside professionals to do the shop drawings. We would review the drawings and approve them, then the cutting drawings were submitted to the site, and they would then cut the stone as per the drawings," Almodovar said. "Each stone was identified, and a number of storage areas were established where palletized material was placed. It was as close to an old method of processing stone in which I have ever taken part. Typically, for our projects we worked with outfits that specialize in architecturally cut stone, and there is a lot of machinery used. On this project, you could go out to the fabricating shop and see these guys, chisel in hand, facing the stone and shaping the stone. I was amazed by the way they were handling the material."In total, the project required 53,000 square feet of stone to be cut, according to King, with 6,000 custom-cut pieces. In all, it took over two years to cut and install the stonework. "It was a very small crew, so it took a considerable amount of time to do all of this work," Holzman explained. "They had people come to work for them just for this project, some students did bits and pieces, but it was a formidable effort over a long period of time." To assist in the fabrication process, a small portion of the sandstone was sent to The Georgia Marble Co. in Tate, GA, for fabrication.
Over the course of the project, the production and installation process was supervised by the University's on-site project manager, Dan Henon, and also by HHPA's construction administrator, Ryan Bussard, who would travel to Sewanee every two weeks. Additionally, Almodovar and Holzman visited the site on a regular basis during the two-year construction period. "Between the University and our office, a lot of time was spent overseeing the installation," Almodovar said.
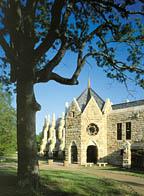
Stone complements
While sandstone is the signature element of McClurg Hall, the building is also composed of other stone materials. Of particular interest, Canadian limestone was used for the decorative finials that sit atop the refectory wing walls. Holzman said the inclusion of these finials helps the building relate to its neighbors on campus. "One of the elements that distinguishes the best buildings on campus are their profiles against the sky," he said. "And the parts that you see are frequently the finials, or the cresting along some of the parapets and cornice work that creates a profile. There was a desire on our part to have elements that were like that in McClurg."The limestone was quarried and fabricated by Gillis Quarries of Winnipeg, Manitoba, Canada. Initially, the architects planned to have each finial carved from a single piece of stone, but for practical reasons, it was done in sections. "We thought that one large piece would be easier to handle because it could just be by crane on top of a standard wing wall," Holzman said. "These elements were about 11 feet tall, and we subsequently discovered that everyone felt it would be considerably easier and more economical if we made them in smaller units. So the finials ended up being made in 3-foot sections that were then assembled to make the larger unit."
A variety of limestone sources had been considered before making the decision to use material from Gillis Quarries. "We used the limestone from Canada because they were eager to do the project and had the ability to meet our schedule and our budget," Holzman said. "They had no difficulty in cutting the shapes that we wanted, and we had previous experience with them."
Slate also was used on McClurg Hall to reflect the campus vernacular. "Being a neighbor to the chapel - and to some of the smaller buildings on campus that are composed not unlike this building - it seemed appropriate to have a slate roof," Holzman said. "We picked a variegated slate because the mottled appearance was more in keeping with the neighboring structures."
With the quarry sites on campus now revived after decades of dormancy, the possibility remains for new projects at the University of the South to use Sewanee stone. "Because it was a start-up after a 20-year hiatus, it may not have been the most economical way to produce this project," Holzman said. "But I think in the future, the value that is added is the potential to use the material on other future projects. As more sophisticated equipment is acquired by the university, they'll be able to do a lot more work on campus."
A lasting impression
Once construction was completed, it was apparent that the architects achieved their goal of creating a building with a Gothic character, but in a modern context. "The Gothic style isn't overwhelming. When you're in the refectory, there is this great sense of light and openness. A curtainwall system perpendicular to the wing walls surrounds the refectory. The openness of this space is surprising. From these spaces there is a very strong connection to the outdoors. With this quantity of stone, you might be concerned with being hermetically sealed off from the rest of the campus, but that's not the case at all," said Holzman.
In the year that has passed since the official dedication of McClurg Hall, the University community has made the facility an integral part of campus life. "I think that the new building has accomplished a number of objectives," Holzman said. "There has been a change in the food service. Everyone on campus uses the building as anticipated, but to an even greater extent than originally imagined. Not only are students coming here, but also is the faculty. People use the building throughout the day. They are studying here and doing a lot of things that we had hoped for. It has brought life to this part of the campus in a way that is different than before."